Good point, I forgot the America fixation for buying nuts and bolts from the cheapest tat suppliers out of China and India bought online or at the nearest shopping "mall" Bolts from supermarkets in buckets.Just my opinion...
But I am not so sure I would use ss bolts in that kind of application....
Unless the bolts are not being overly stressed, then it should be fine.
If you do. I would run a die over the new SS bolts. It tends to be a smoother thread. And less chance of galling....
Take note from now on when I reference nuts and bolts in general I really mean these folk for you lot. Unbrako
Catalog & Downloads | Unbrako
unbrako catalog, unbrako catalogue, unbrako engineering guide, fastener guide, case studies about unbrako

In addition also note the threaded bolt holes on the back of the SA-3 and SA_6 block for the heads have inserted stainless steel helicoils and these folk apply:
HELICOIL® – Thread inserts for metals | Böllhoff
HELICOIL® thread inserts reinforce and repair thread. Discover our product variants for different requirements.

It is also prudent to use a small amount of even the cheap "Copperslip" from your local supermarket or
if your budget reaches the likes of Swagelok Goop
And if the budget is exceeded and the wife doesn't know try Rocol Anti Seize stainless
Anti-Seize Paste Specifically Designed for Nimonic and Stainless Steel - ANTI-SEIZE Stainless - ROCOL - ROCOL
Nickel-free stainless steel anti-seize, designed for stainless, nimonic and silver-coated fasteners. Ideal for use at high temperatures over long periods.
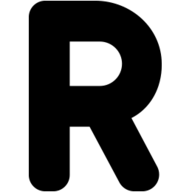
And for those who really want to know it goes by the uninspiring name of Rocol SA-610 Go figure LOL
