brtlmj
Registered
Searching scubaboard returns a number of references to homemade yoke nut sockets. Sadly, references are all I could find; all the links are dead. So, I had to figure it out myself, and I thought I would share.
You will need:
Drill a 17/64 hole through the 3/4'' socket. You want the top of the hole to almost touch the solid part of the socket. That places the ceter of the hole some 15 mm from the top. (Sorry for mixing units. I am a metric guy with SAE tools)
Using a bench grinder:
(We are doing it so that the socket can go as low as possible and grab the entire nut, not half of it.)
Using a dremel or similar tool with a grinder bit remove all sharp edges.
Now take the 1/4 extension and start grinding the "female" end. You want it to become a square that fits tightly into the 3/8 drive (roughly 9.6mm across). When it fits, cut it off from the rest of the extension.
Don't make it too long - you only want enough so that when it is flush with the top of the socket, it does not cover the two holes you drilled.
Epoxy the insert you made in the 3/4 socket.
All done!
Now, to assemble a regulator, you would use your new socket with a 1/4'' extension and a torque wrench. It should easily handle the torque needed.
To remove a yoke nut, especially one that has been in there for a while, you may need more torque than a 1/4'' extension can handle. That's what the two holes are for. Simply put the socket in place and hold it there with the yoke screw:
Then clamp the whole regulator in a soft jaw vise, put a 1/4'' steel rod through the two holes, and you should be able to apply as much torque as you need.
You will need:
- 3/4'' six point low profile socket, 3/8'' drive. Do not get a 12-point socket - with the soft brass the nut is made of, you need all the contact area you can get. Craftsman 43007 would work. $3 on eBay.
- 1/4 drive, three inch (the exact length does not matter, but three inches or more make it easier to handle the piece) extension. $2 on eBay.
- epoxy

Drill a 17/64 hole through the 3/4'' socket. You want the top of the hole to almost touch the solid part of the socket. That places the ceter of the hole some 15 mm from the top. (Sorry for mixing units. I am a metric guy with SAE tools)
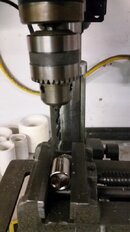
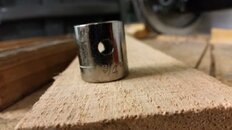
Using a bench grinder:
- remove 2mm or so from the 3/4'' socket
- make a 45 degree cut around the socket
- go a little deeper at the two points 90 degrees from the two holes you drilled before
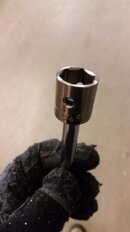
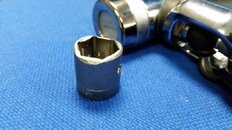
(We are doing it so that the socket can go as low as possible and grab the entire nut, not half of it.)
Using a dremel or similar tool with a grinder bit remove all sharp edges.
Now take the 1/4 extension and start grinding the "female" end. You want it to become a square that fits tightly into the 3/8 drive (roughly 9.6mm across). When it fits, cut it off from the rest of the extension.
Don't make it too long - you only want enough so that when it is flush with the top of the socket, it does not cover the two holes you drilled.
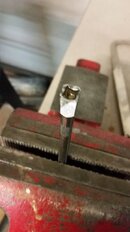
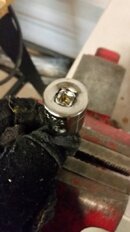
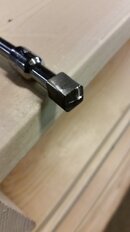
Epoxy the insert you made in the 3/4 socket.
All done!
Now, to assemble a regulator, you would use your new socket with a 1/4'' extension and a torque wrench. It should easily handle the torque needed.
To remove a yoke nut, especially one that has been in there for a while, you may need more torque than a 1/4'' extension can handle. That's what the two holes are for. Simply put the socket in place and hold it there with the yoke screw:
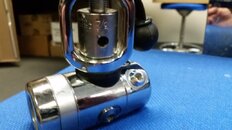
Then clamp the whole regulator in a soft jaw vise, put a 1/4'' steel rod through the two holes, and you should be able to apply as much torque as you need.